
Lasersko rezanjeje revolucioniral način, kako industrija reže in oblikuje različne materiale.To je zelo natančen in učinkovit postopek, ki uporablja visoko zmogljive laserje za rezanje različnih materialov z izjemno visoko natančnostjo.Ta vrhunska tehnologija je postala stalnica v proizvodni, avtomobilski, vesoljski in drugih industrijah.V tem članku bomo raziskali postopek laserskega rezanja, uporabljena orodja in stroje ter njegove prednosti pred tradicionalnimi metodami rezanja.
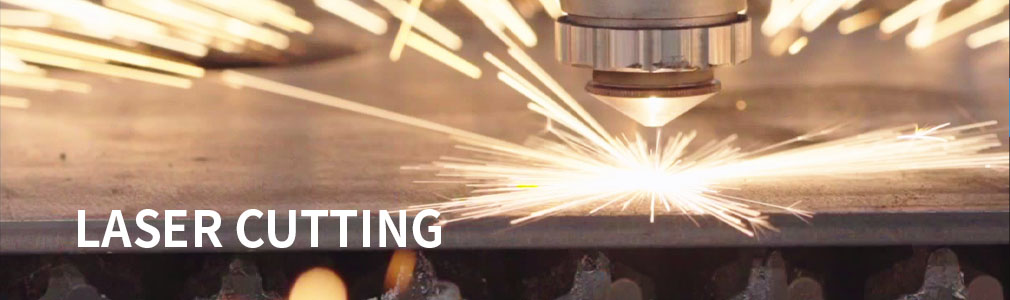
Thelasersko rezanjepostopek vključuje uporabo usmerjenega laserskega žarka za rezanje različnih materialov.Laserski žarek oddaja laserski rezalni stroj in ga običajno krmili računalnik.Laserski žarek je usmerjen na material, ki ga režemo, in intenzivna toplota, ki jo ustvari laser, uparja, stopi ali zažge material po vnaprej določeni poti.Posledica tega so čisti, natančni rezi in zmanjšanje toplotno prizadetih območij in materialnih odpadkov.
Obstaja veliko različnih vrst laserskih rezalnikov, od katerih ima vsak svojo specifično uporabo in prednosti.Najpogostejši tipi vključujejo CO2 laserje, laserje z vlakni in neodimove (Nd) laserje.CO2 laserji se pogosto uporabljajo za rezanje nekovinskih materialov, kot so les, plastika in akril, medtem ko so laserji z optičnimi vlakni in Nd laserji primernejši za rezanje kovin in zlitin.
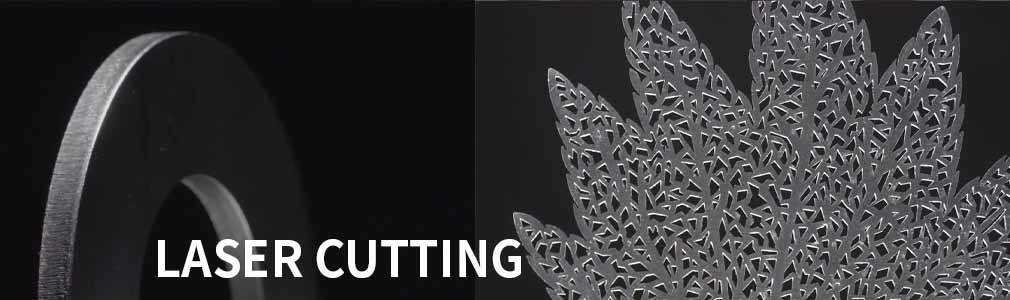
Thepostopek laserskega rezanjase začne z zasnovo dela ali komponente, ki jo je treba rezati.Načrt se nato vnese v program za računalniško podprto načrtovanje (CAD), ki ustvari digitalno datoteko, ki vsebuje poti za laserske reze.Ta digitalna datoteka se nato prenese v laserski rezalnik, ki uporablja datoteko za vodenje laserskega žarka po vnaprej določeni poti za rezanje materiala.
Ena od glavnih prednosti laserskega rezanja je možnost izdelave zelo natančnih in kompleksnih rezov z minimalno porabo materiala.To stopnjo natančnosti je težko doseči s tradicionalnimi metodami rezanja, kot so žage ali škarje, kar lahko povzroči grobe in nenatančne robove.Poleg tega je mogoče lasersko rezanje uporabiti za rezanje različnih materialov, vključno s kovinami, plastiko, keramiko in kompoziti, zaradi česar je vsestranska in stroškovno učinkovita rešitev za številne industrije.
Postopek laserskega rezanja ponuja tudi številne druge prednosti pred tradicionalnimi metodami rezanja.Na primer, lasersko rezanje je brezkontaktni postopek, kar pomeni, da material, ki ga režemo, ni izpostavljen mehanski sili ali pritisku, kar povzroči manj popačenj in deformacij.Poleg tega je toplotno prizadeto območje, ki nastane z laserskim rezanjem, zelo majhno, kar pomeni, da okoliški materiali niso izpostavljeni prekomerni vročini, kar zmanjšuje tveganje zvijanja ali drugih toplotnih učinkov.
Poleg tegalasersko rezanjeje učinkovit postopek, ki zahteva minimalno nastavitev in čas izvedbe.Za razliko od tradicionalnih metod rezanja, ki lahko zahtevajo uporabo več orodij in nastavitev, je mogoče lasersko rezanje hitro in preprosto programirati za rezanje različnih delov in komponent.Zaradi tega je idealna rešitev za podjetja, ki želijo poenostaviti proizvodne procese in zmanjšati proizvodne stroške.
Če povzamemo, je postopek laserskega rezanja zelo natančna in učinkovita metoda, ki jo je mogoče uporabiti za rezanje različnih materialov.Ponuja veliko prednosti pred tradicionalnimi metodami rezanja, vključno z vrhunsko natančnostjo, minimalno količino odpadnega materiala in zmanjšanimi toplotnimi vplivi.Ker tehnologija laserskega rezanja še naprej napreduje, bo verjetno ostal ključni proces za številne industrije v prihodnjih letih.Ne glede na to, ali ste proizvajalec, oblikovalec ali inženir, lahko lasersko rezanje spremeni vaš način dela.
Čas objave: 23. januarja 2024