
Laser cleaning technology utilizes narrow pulse width, high power density lasers on the surface of the object to be cleaned. Through the combined effects of rapid vibration, vaporization, decomposition, and plasma peeling, contaminants, rust stains, or coatings on the surface undergo instant evaporation and detachment, achieving surface cleaning.
Laser cleaning offers advantages such as non-contact, environmentally friendly, efficient precision, and no damage to the substrate, making it applicable in various scenarios.

Green and Efficient
The tire industry, new energy industry, and construction machinery industry, among others, widely apply laser cleaning. In the era of the "dual carbon" goals, laser cleaning is emerging as a new solution in the traditional cleaning market due to its high efficiency, precise controllability, and environmentally friendly characteristics.
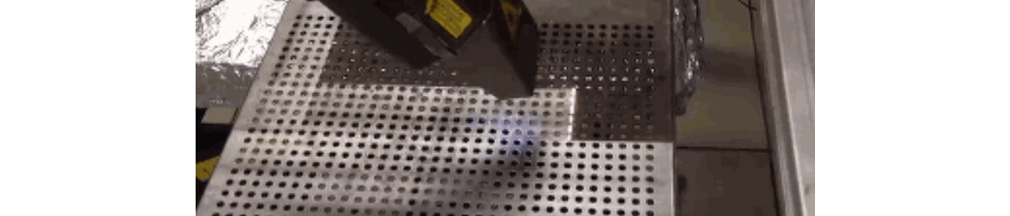
Concept of Laser Cleaning:
Laser cleaning involves focusing laser beams on the material surface to rapidly vaporize or peel off surface contaminants, achieving material surface cleaning. Compared to various traditional physical or chemical cleaning methods, laser cleaning is characterized by no contact, no consumables, no pollution, high precision, and minimal or no damage, making it an ideal choice for the new generation of industrial cleaning technology.
Principle of Laser Cleaning:
The principle of laser cleaning is complex and may involve both physical and chemical processes. In many cases, physical processes dominate, accompanied by partial chemical reactions. The main processes can be categorized into three types: vaporization process, shock process, and oscillation process.
Gasification Process:
When high-energy laser irradiation is applied to the surface of a material, the surface absorbs the laser energy and converts it into internal energy, causing the surface temperature to rapidly increase. This rise in temperature reaches or exceeds the vaporization temperature of the material, causing the contaminants to detach from the material surface in the form of vapor. Selective vaporization often occurs when the absorption rate of the contaminants to the laser is significantly higher than that of the substrate. A typical application example is the cleaning of dirt on stone surfaces. As shown in the diagram below, contaminants on the stone surface strongly absorb the laser and are quickly vaporized. Once the contaminants are completely removed, and the laser irradiates the stone surface, the absorption is weaker, and more laser energy is scattered by the stone surface. Consequently, there is minimal change in the temperature of the stone surface, thereby protecting it from damage.
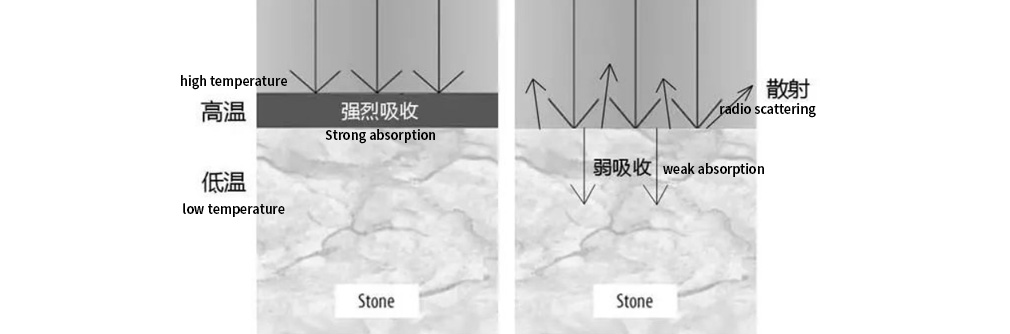
A typical process primarily involving chemical action occurs when cleaning organic contaminants with ultraviolet wavelength lasers, a process known as laser ablation. Ultraviolet lasers have shorter wavelengths and higher photon energy. For example, a KrF excimer laser with a wavelength of 248 nm has a photon energy of 5 eV, which is 40 times higher than that of CO2 laser photons (0.12 eV). Such high photon energy is sufficient to break the molecular bonds in organic materials, causing the C-C, C-H, C-O, etc., bonds in the organic contaminants to fracture upon absorbing the photon energy of the laser, leading to pyrolytic gasification and removal from the surface.
Shock Process in Laser Cleaning:
The shock process in laser cleaning involves a series of reactions that occur during the interaction between the laser and the material, resulting in shock waves impacting the material's surface. Under the influence of these shock waves, surface contaminants shatter into dust or fragments, peeling away from the surface. The mechanisms causing these shock waves are varied, including plasma, vapor, and rapid thermal expansion and contraction phenomena.
Taking plasma shock waves as an example, we can briefly understand how the shock process in laser cleaning removes surface contaminants. With the application of ultra-short pulse width (ns) and ultra-high peak power (107– 1010 W/cm2) lasers, the surface temperature can rise sharply to vaporization temperatures even if the surface absorption of the laser is weak. This rapid temperature increase forms vapor above the material's surface, as shown in the illustration (a). The vapor temperature can reach 104 – 105 K, enough to ionize the vapor itself or the surrounding air, forming a plasma. The plasma blocks the laser from reaching the material surface, possibly halting surface vaporization. However, the plasma continues to absorb laser energy, further increasing its temperature and creating a localized state of extremely high temperature and pressure. This generates a momentary impact of 1-100 kbar on the material surface and progressively transmits inward, as shown in illustrations (b) and (c). Under the impact of the shock wave, surface contaminants fracture into tiny dust, particles, or fragments. When the laser moves away from the irradiated location, the plasma disappears promptly, creating a local negative pressure, and the particles or fragments of the contaminants are removed from the surface, as shown in illustration (d).
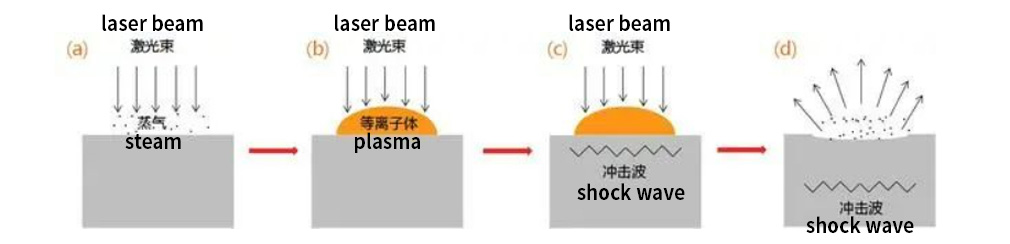
Oscillation Process in Laser Cleaning:
In the oscillation process of laser cleaning, both the heating and cooling of the material occur extremely rapidly under the influence of short-pulse lasers. Due to the different thermal expansion coefficients of various materials, the surface contaminants and the substrate undergo high-frequency thermal expansion and contraction of varying degrees when exposed to short-pulse laser irradiation. This leads to an oscillatory effect that causes the contaminants to peel off from the material surface.
During this peeling process, material vaporization might not occur, nor is plasma necessarily formed. Instead, the process relies on the shear forces generated at the interface between the contaminant and the substrate under the oscillatory action, which break the bond between them. Studies have shown that slightly increasing the angle of laser incidence can enhance the contact between the laser, the particulate contaminants, and the interface of the substrate. This approach lowers the threshold for laser cleaning, making the oscillatory effect more pronounced and improving cleaning efficiency. However, the angle of incidence should not be too large, as a very high angle can reduce the energy density acting on the material surface, thereby weakening the cleaning capability of the laser.
Industrial Applications of Laser Cleaning:
1: Mold Industry
Laser cleaning enables non-contact cleaning for molds, ensuring the safety of mold surfaces. It guarantees precision and can clean sub-micron-level dirt particles that traditional cleaning methods may struggle to remove. This achieves true pollution-free, efficient, and high-quality cleaning.
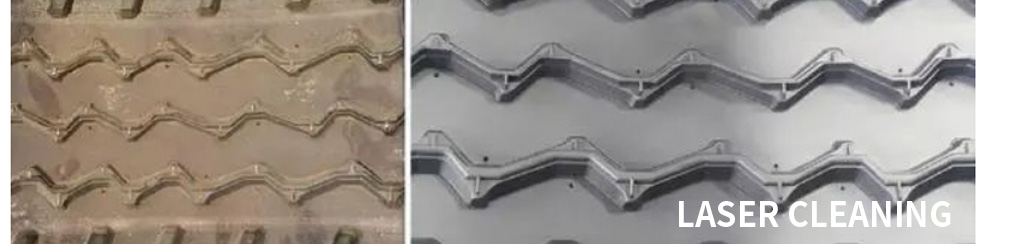
2: Precision Instrument Industry
In precision mechanical industries, components often need to have esters and mineral oils used for lubrication and corrosion resistance removed. Chemical methods are commonly employed for cleaning, but they often leave residues. Laser cleaning can completely remove esters and mineral oils without damaging the surface of the components. Laser-induced explosions of oxide layers on the component surfaces result in shock waves, causing the removal of contaminants without mechanical interaction.
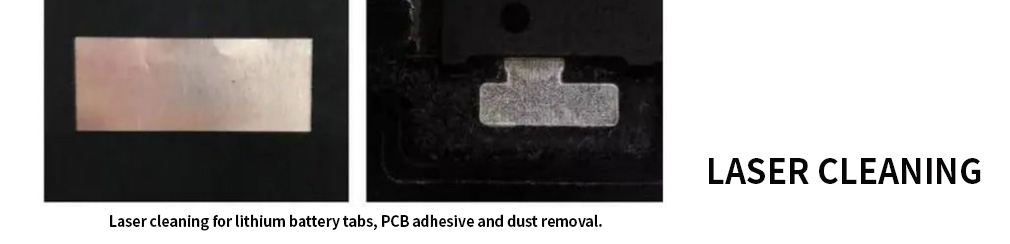
3: Rail Industry
Currently, rail cleaning before welding predominantly uses wheel grinding and sanding, leading to severe substrate damage and residual stress. Moreover, it consumes a significant amount of abrasive consumables, resulting in high costs and serious dust pollution. Laser cleaning can provide a high-quality, efficient, and environmentally friendly cleaning technique for the production of high-speed railway tracks in China. It addresses issues such as seamless rail holes, gray spots, and welding defects, enhancing the stability and safety of high-speed railway operations.
4: Aviation Industry
Aircraft surfaces need to be repainted after a certain period, but before painting, the old paint must be completely removed. Chemical immersion/wiping is a major paint stripping method in the aviation sector, causing substantial chemical waste and an inability to achieve localized paint removal for maintenance. Laser cleaning can achieve high-quality removal of paint from the aircraft skin surface and is easily adaptable to automated production. Currently, this technology has begun to be applied in the maintenance of some high-end aircraft models abroad.
5: Maritime Industry
Pre-production cleaning in the maritime industry commonly uses sandblasting methods, causing severe dust pollution to the surrounding environment. As sandblasting is gradually being prohibited, it has led to reduced production or even shutdowns for shipbuilding companies. Laser cleaning technology will provide a green and pollution-free cleaning solution for the anti-corrosion coating of ship surfaces.
由用户整理投稿发布,不代表本站观点及立场,仅供交流学习之用,如涉及版权等问题,请随时联系我们(yangmei@bjjcz.com),我们将在第一时间给予处理。
Post time: Jan-16-2024