
Laser cutting has revolutionized the way the industry cuts and shapes different materials. This is a high-precision, efficient process that utilizes high-power lasers to cut a variety of materials with extremely high precision. This cutting-edge technology has become a staple in manufacturing, automotive, aerospace and other industries. In this article, we’ll explore the laser cutting process, the tools and machines used, and its advantages over traditional cutting methods.
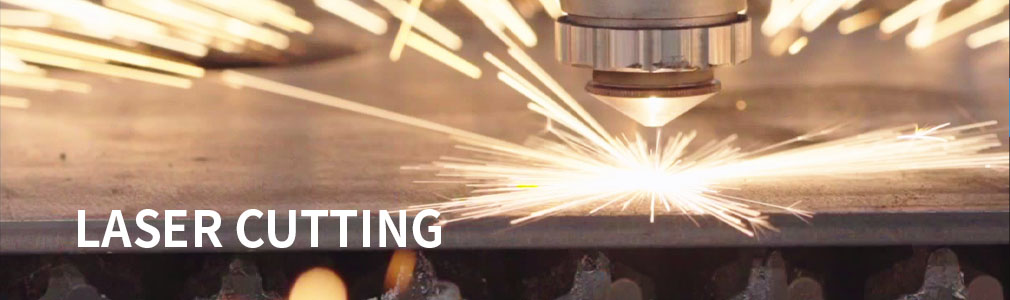
The laser cutting process involves using a focused laser beam to cut various materials. The laser beam is emitted from a laser cutting machine and is usually controlled by a computer. The laser beam is directed onto the material being cut, and the intense heat generated by the laser vaporizes, melts or burns the material along a predetermined path. This results in clean, precise cuts and minimizes heat-affected zones and material waste.
There are many different types of laser cutters, each with their own specific uses and benefits. The most common types include CO2 lasers, fiber lasers, and neodymium (Nd) lasers. CO2 lasers are widely used for cutting non-metallic materials such as wood, plastic and acrylic, while fiber optic and Nd lasers are more suitable for cutting metals and alloys.
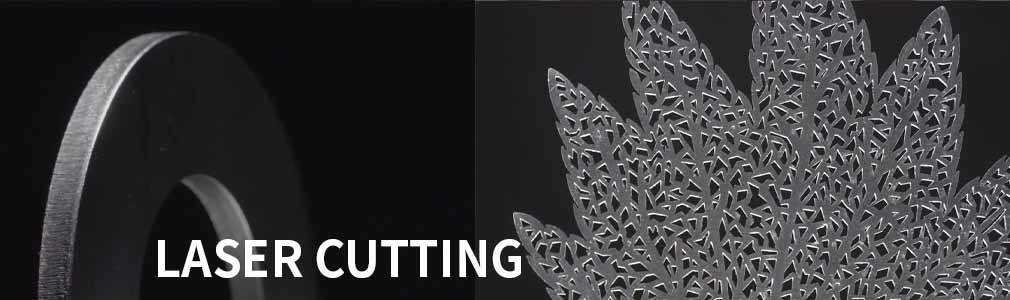
The laser cutting process begins with the design of the part or component to be cut. The design is then entered into a computer-aided design (CAD) program, which creates a digital file containing the paths for the laser cuts. This digital file is then transferred to the laser cutter, which uses the file to guide the laser beam along a predetermined path to cut the material.
One of the main advantages of laser cutting is the ability to make highly precise and complex cuts with minimal material waste. This level of precision is difficult to achieve using traditional cutting methods such as saws or shears, which can result in rough and inaccurate edges. Additionally, laser cutting can be used to cut a variety of materials, including metals, plastics, ceramics, and composites, making it a versatile and cost-effective solution for many industries.
The laser cutting process also offers several other advantages over traditional cutting methods. For example, laser cutting is a non-contact process, which means that the material being cut is not subjected to mechanical force or pressure, resulting in less distortion and deformation. Additionally, the heat-affected zone created by laser cutting is very small, meaning that surrounding materials are not exposed to excessive heat, minimizing the risk of warping or other thermal effects.
Additionally, laser cutting is an efficient process that requires minimal setup and lead time. Unlike traditional cutting methods that may require the use of multiple tools and setups, laser cutting can be quickly and easily programmed to cut a variety of parts and components. This makes it an ideal solution for companies looking to streamline production processes and reduce manufacturing costs.
In summary, the laser cutting process is a highly precise and efficient method that can be used to cut a variety of materials. It offers many advantages over traditional cutting methods, including superior accuracy, minimal material waste, and reduced heat-affected zones. As laser cutting technology continues to advance, it is likely to remain a key process for many industries in the coming years. Whether you're a manufacturer, designer or engineer, laser cutting has the potential to change the way you work.
由用户整理投稿发布,不代表本站观点及立场,仅供交流学习之用,如涉及版权等问题,请随时联系我们(yangmei@bjjcz.com),我们将在第一时间给予处理。
Post time: Jan-23-2024